Planning deliveries by zone is costing you money
- Jesse Treharne
- Apr 14, 2021
- 3 min read
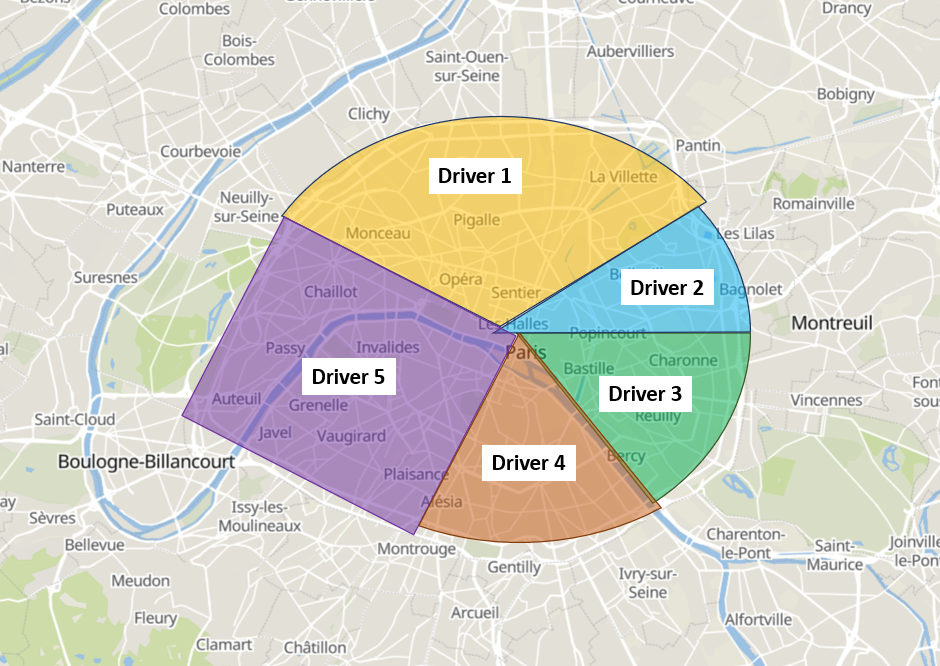
If you've worked in last-mile logistics, you're probably already familiar with the idea of Zones.
Different companies call them different things - Vehicle Sectors, Planning Regions, Delivery Areas, etc - but the idea is the same
The geographic area where the customer is located determines the vehicle or driver that visits it.
But in most cases, using zones costing you money!
Everyone is doing it
Almost every logistics company in the world operates like this... or at least they used to.
Why?
Because it's easy.
Let's imagine what happens when a new order arrives from one of your customers...
The dispatcher receives the order.
The dispatcher looks up the address. Ahhh, yes, it's in Bastille, that's in Zone 3.
The dispatcher checks who's doing Zone 3 tomorrow. Great - it's Driver 3.
The dispatcher check's how many Jobs Driver 3 has to do tomorrow. Perfect, she should have time to make this delivery between the delivery in Charonne and the delivery in Popincourt.

This workflow varies slightly between logistics companies...
Some have software to lookup the address...
Others automatically categorise it into the correct zone...
and sometimes the Driver is responsible for figuring out when they have time to perform the new delivery.
Does this workflow sound familiar?
Only Human

The main reason we do this is because it fits inside our brains.
We can easily understand why this driver is making that specific delivery.
And it's also historical. Before everyone had GPS navigation, it was also useful to have drivers that know their area well.
But it's not the 80s anymore. So does it still make sense?
The Real World
Times change. Technology advances. Yet many logistics companies hold on to their old habits.
But this old habit leaves them behind the competition.
Why? Because delivery zones don't reflect the real world.
Zones don't reflect the real world
One way streets.
Highways.
Traffic.
Changing order volumes.
Vehicle capacities.
Opening hours.
Appointments.
All of these things mean that perfect-looking "flower petal" delivery routes may not be a rose among the thorns. They place arbitrary restrictions on who can deliver what, which means that your drivers are driving more than they need to.
Your drivers are driving more than they need to.
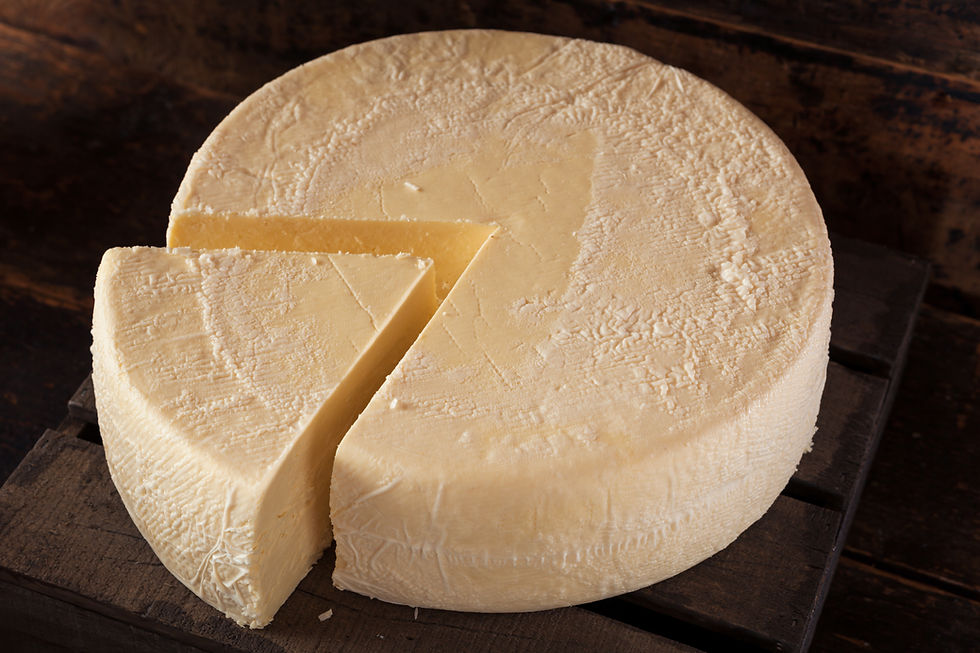
Efficiency Matters
Usually, Removing zones reduces kilometres driven by 20% or more. These arbitrary geographic boundaries are a bad thing.
We know this for a fact, because we have measured the improvement that our customers receive using our last-mile route optimisation SaaS platform. Our platform can optimise delivery routes with or without zones, making it easy for you to see how much you could save by removing zones from your workflow.
Removing zones reduces kilometres driven by 20%
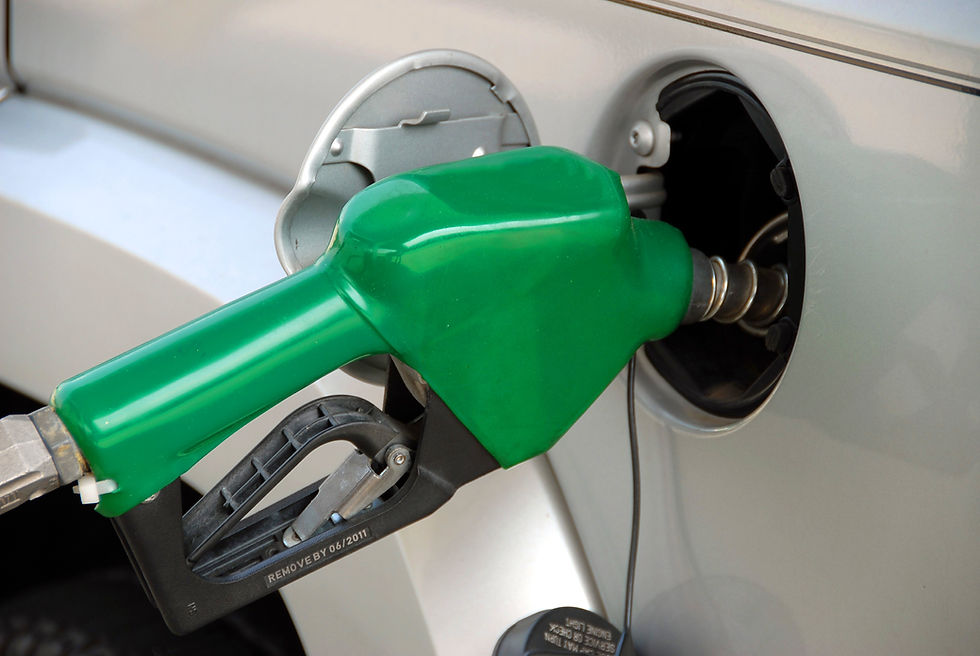
But we know that change can be difficult in large organisations. So it's important to understand the concrete value to the business before taking the leap.
That's the way we've always done it
For some logistics companies, there are real constraints which make the transition away from delivery zones more difficult.
Especially if you run a cross-dock warehouse, or you have tight order cutoffs.
This is because you don't know which dock to put the parcel on until the driving routes are planned. And if there are no zones, then you may have to wait until the last order is placed before planning driving routes.
In cases like this, it's important to understand and quantify the impact.
Ask yourself the question: If we moved our last-order cutoff 30 minutes earlier:
how would that impact our customers?
would that give us enough time to sort orders onto the correct dock based after planning routes?
how much would we save from driving more efficient routes?
For some companies, the answer is no. However, for most last-mile logistics companies, there's only one very expensive reason they don't change...

"That's the way we've always done it."
Comments